During the injection molding process, it is common to encounter various defects in molded parts, which can impact the quality and performance of the products. This article aims to explore some of the common defects in injection molded parts and discuss methods to address these issues.
1.Flow Marks:
Flow lines are cosmetic defects characterized by off-color lines, streaks, or patterns that become visible on the surface of a molded part. These lines occur when the molten plastic moves at varying speeds throughout the injection mold, resulting in different rates of resin solidification. Flow lines are often an indication of low injection speed and/or pressure.
Additionally, flow lines can arise when the thermoplastic resin flows through areas of the mold with varying wall thicknesses. Therefore, maintaining consistent wall thickness and ensuring appropriate lengths of chamfers and fillets are crucial to minimize the occurrence of flow lines. Another effective measure is placing the gate in a thin-walled section of the tool cavity, which helps to reduce the formation of flow lines.
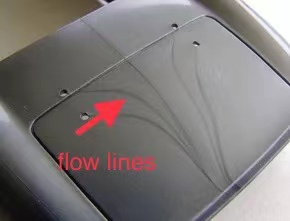
2. Surface Delamination:
Delamination refers to the separation of thin layers on the surface of a part, resembling peelable coatings. This condition occurs due to the presence of non-bonding contaminants in the material, leading to localized faults. Delamination can also be caused by excessive reliance on mold release agents.
To address and prevent delamination, it is recommended to raise mold temperatures and optimize the mold ejection system to minimize the reliance on mold release agents, as these agents can contribute to delamination. Additionally, thorough pre-drying of the plastic prior to molding can aid in preventing delamination.
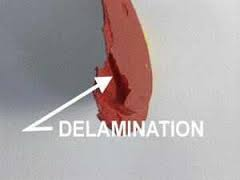
3.Knit lines:
Knit lines, also known as weld lines, are defects that occur when two flows of molten resin converge as they move through the mold geometry, particularly around areas with holes. When the plastic flows and wraps around each side of a hole, the two flows meet. If the temperature of the molten resin is not optimal, the two flows may fail to bond properly, resulting in a visible weld line. This weld line diminishes the overall strength and durability of the component.
To prevent the premature solidification process, it is beneficial to increase the temperature of the molten resin. Moreover, raising the injection speed and pressure can also help mitigate the occurrence of knit lines. Resins with lower viscosity and lower melting points are less susceptible to weld line formation during injection molding. Additionally, removing partitions from the mold design can eliminate the formation of weld lines.
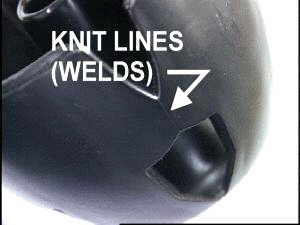
4.Short Shots:
Short shots occur when the resin fails to completely fill the mold cavity, resulting in incomplete and unusable parts. Various factors can cause short shots in injection molding. Common causes include restricted flow within the mold, which can be attributed to narrow or blocked gates, trapped air pockets, or insufficient injection pressure. Material viscosity and mold temperature can also contribute to short shots.
To prevent the occurrence of short shots, it is beneficial to increase the mold temperature, as this can improve resin flow. Additionally, incorporating additional venting into the mold design allows trapped air to escape more effectively. By addressing these factors, the likelihood of short shots in injection molding can be minimized.
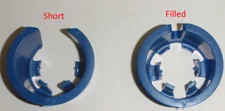
5.Warping:
Warping in injection molding refers to unintended twists or bends in a part caused by uneven internal shrinkage during the cooling process. This defect typically arises from non-uniform or inconsistent mold cooling, leading to the generation of internal stresses within the material.To prevent warping defects in injection molding, it is essential to ensure that parts are adequately cooled at a gradual rate, allowing sufficient time for the material to cool uniformly. Maintaining a uniform wall thickness in the mold design is crucial for several reasons, including facilitating the smooth flow of plastic through the mold cavity in a consistent direction.By implementing proper cooling strategies and designing molds with uniform wall thickness, the risk of warpage defects in injection molding can be minimized, resulting in high-quality and dimensionally stable parts.
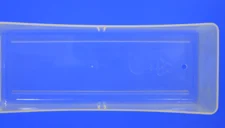
6.Jetting:
Jetting defects in injection molding can occur when the solidification process is uneven. Jetting happens when the initial resin jet enters the mold and starts to solidify before the cavity is completely filled. This results in visible squiggly flow patterns on the surface of the part and reduces its strength.
To prevent jetting defects, it is recommended to reduce the injection pressure, ensuring a more gradual fill of the mold. Increasing the mold and resin temperature can also help prevent premature solidification of the resin jets. Additionally, placing the injection gate in a way that directs the flow of material through the shortest axis of the mold is an effective method for minimizing jetting.
By implementing these measures, the risk of jetting defects in injection molding can be reduced, leading to improved surface quality and enhanced part strength.
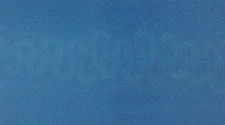
Our company takes multiple measures to prevent injection molding defects and ensure high-quality injection molded parts. Key aspects include selecting premium materials, meticulous mold design, precise control of process parameters, and strict quality control. Our team undergoes professional training and continuously improves and optimizes the production process.
Our company takes multiple measures to prevent injection molding defects and ensure high-quality injection molded parts. Key aspects include selecting premium materials, meticulous mold design, precise control of process parameters, and strict quality control. Our team undergoes professional training and continuously improves and optimizes the production process.
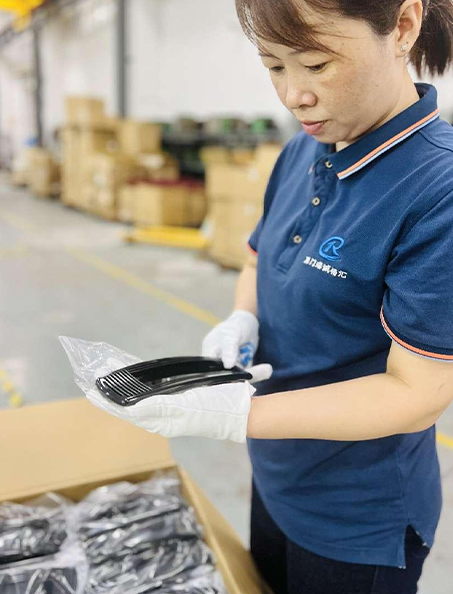
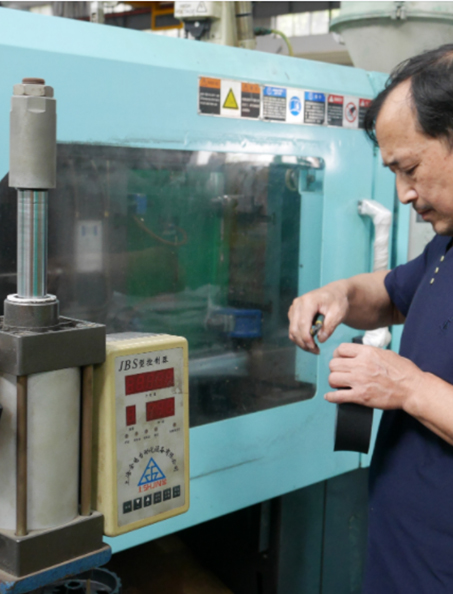
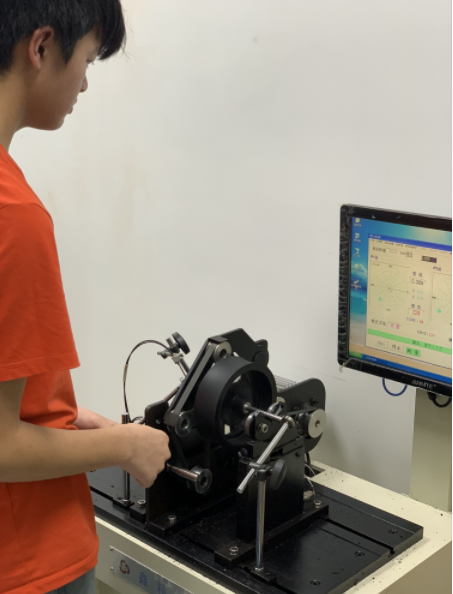
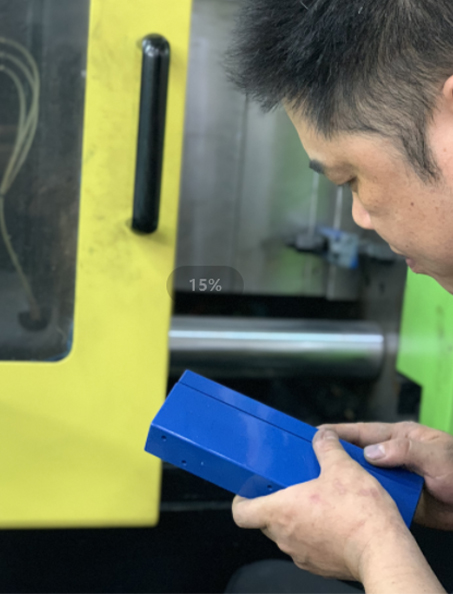
Our company ensures product quality by following the ISO 9001 quality management system. We have established a comprehensive quality management system with standardized procedures and processes. We encourage employee participation and provide training and education. Through these measures, we guarantee that our shipped products have excellent quality and meet customer demands.
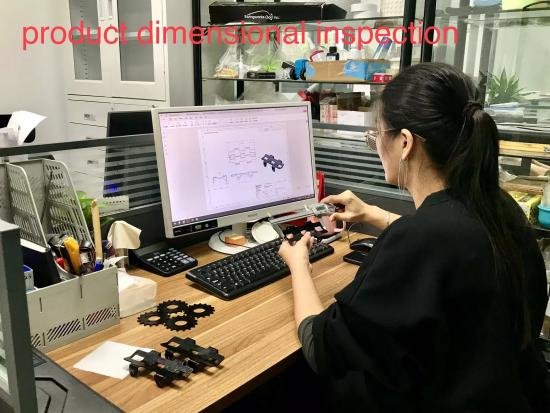
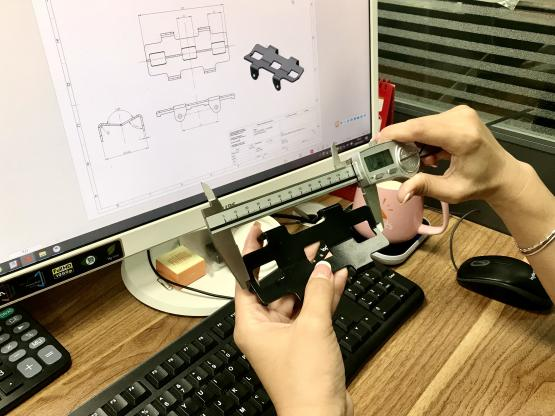
Opting for a manufacturing partner such as xiamenruicheng, who possesses extensive knowledge of typical injection molding defects and their resolution, can make a significant impact on the outcome of your project. It can be the determining factor between obtaining high-quality parts, delivered on schedule and within budget, or encountering issues like weld lines, jetting, flash, sink marks, and other flaws. Besides our expertise as an established on-demand manufacturing shop, we also offer design consultation and optimization services. This ensures that we assist every team in creating functional, aesthetically pleasing, and high-performance parts with utmost efficiency. Get in touch with us today to explore our comprehensive injection molding solutions.
Post time: Dec-15-2023