ප්ලාස්ටික් ආලේපනය යනු ඉලෙක්ට්රොනික කර්මාන්තය, ආරක්ෂක පර්යේෂණ, ගෘහ උපකරණ සහ දෛනික අවශ්යතා සඳහා බහුලව භාවිතා වන ආලේපන ක්රියාවලියකි.ප්ලාස්ටික් ආලේපන ක්රියාවලිය යෙදීමෙන් ලෝහ ද්රව්ය විශාල ප්රමාණයක් ඉතිරි වී ඇති අතර, එහි සැකසුම් ක්රියාවලිය සරල වන අතර ලෝහ ද්රව්ය හා සසඳන විට එහි බර අඩු බැවින් ප්ලාස්ටික් ආලේපන ක්රියාවලියෙන් නිපදවන උපකරණවල බර ද අඩු වේ. වැඩි යාන්ත්රික ශක්තියක් සහිත ප්ලාස්ටික් කොටස් පෙනුම, වඩා ලස්සන හා කල් පවතින.
ප්ලාස්ටික් ආලේපනයේ ගුණාත්මකභාවය ඉතා වැදගත් වේ.ප්ලාස්ටික් ආලේපනයේ ගුණාත්මකභාවය කෙරෙහි සැලකිය යුතු බලපෑමක් ඇති කළ හැකි ප්ලාස්ටික් ආලේපන ක්රියාවලිය, ක්රියාකාරීත්වය සහ ප්ලාස්ටික් ක්රියාවලිය ඇතුළුව ප්ලාස්ටික් ආලේපනයේ ගුණාත්මක භාවයට බලපාන බොහෝ සාධක තිබේ.
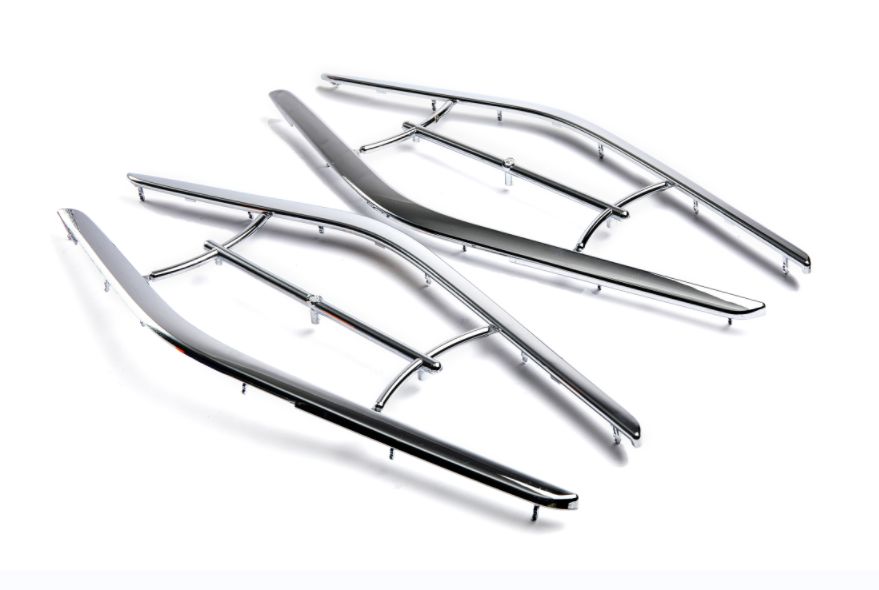
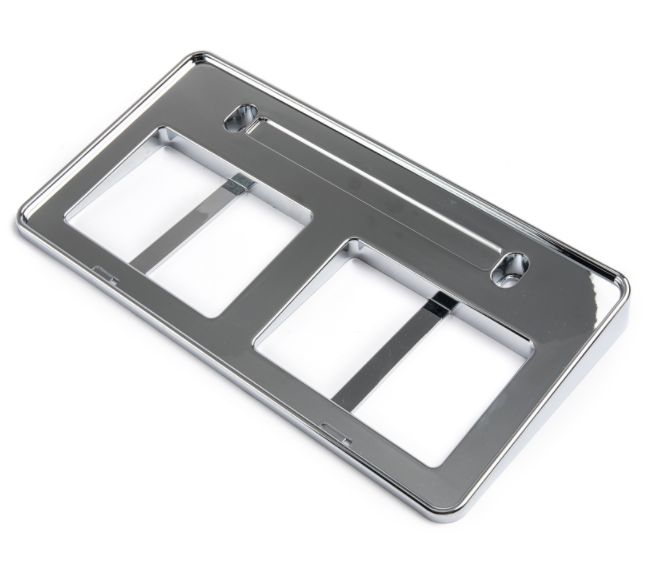
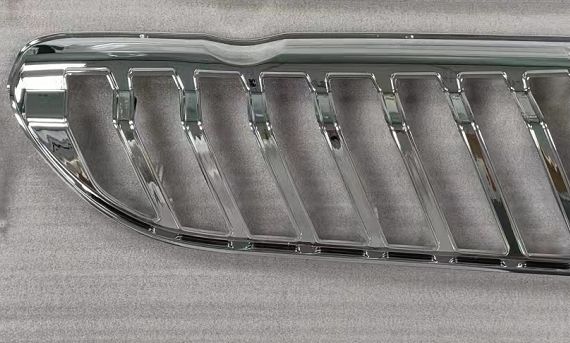
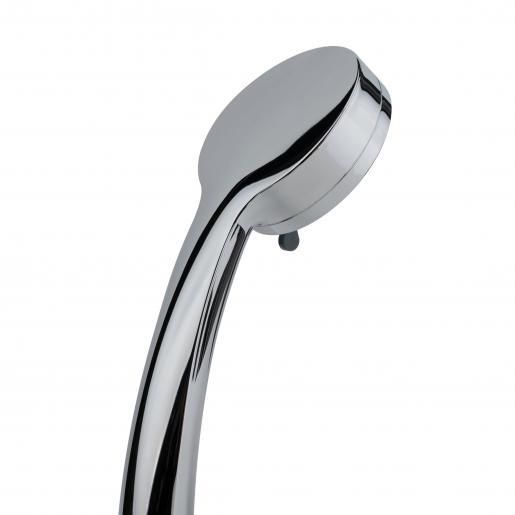
1. අමු ද්රව්ය තෝරාගැනීම
වෙළඳපොලේ විවිධ ප්ලාස්ටික් වර්ග රාශියක් ඇත, නමුත් සෑම ප්ලාස්ටික් වර්ගයකටම ආවේණික වූ ගුණාංග ඇති බැවින් ඒවා සියල්ලම තහඩු කළ නොහැක, සහ තහඩු දැමීමේදී ප්ලාස්ටික් සහ ලෝහ ස්ථරය අතර ඇති බැඳීම සහ භෞතික ගුණාංග අතර සමානකම සලකා බැලිය යුතුය. ප්ලාස්ටික් සහ ලෝහ ආලේපනය.ප්ලේට් කිරීම සඳහා දැනට පවතින ප්ලාස්ටික් ABS සහ PP වේ.
2.කොටස්වල හැඩය
ඒ).ප්ලාස්ටික් කොටස හැකිලීමට හේතු වන අසමානතාවය වළක්වා ගැනීම සඳහා ප්ලාස්ටික් කොටසෙහි ඝනකම ඒකාකාරී විය යුතුය, ආලේපනය අවසන් වූ විට, එහි ලෝහමය දීප්තිය එකවරම හැකිලීමට හේතු වේ.
තවද ප්ලාස්ටික් කොටසෙහි බිත්තිය ඉතා සිහින් නොවිය යුතුය, එසේ නොමැතිනම් එය ආලේපනය කිරීමේදී පහසුවෙන් විකෘති වන අතර ආලේපනයේ බන්ධනය දුර්වල වනු ඇත, දෘඪතාව අඩු වන අතර භාවිතයේදී ආලේපනය පහසුවෙන් වැටෙනු ඇත.
බී).අන්ධ සිදුරු වලින් වළකින්න, එසේ නොමැති නම් අන්ධ සොලෙනොයිඩ් වල ඉතිරිව ඇති ප්රතිකාර ද්රාවණය පහසුවෙන් පිරිසිදු කළ නොහැකි අතර ඊළඟ ක්රියාවලියේදී දූෂණය වීමට හේතු වන අතර එමඟින් ආලේපන ගුණාත්මක භාවයට බලපායි.
C).ප්ලේටින් තියුණු දාර සහිත නම්, තහඩු කිරීම වඩාත් අපහසු වනු ඇත, තියුණු දාර බලශක්ති උත්පාදනයට පමණක් නොව, තහඩුව කොන් වල ඉදිමීමට ද හේතු වනු ඇත, එබැවින් ඔබ අරයක් සහිත වටකුරු කෙළවරක් තෝරා ගැනීමට උත්සාහ කළ යුතුය. අවම වශයෙන් 0.3 මි.මී.
පැතලි ප්ලාස්ටික් කොටස් ප්ලේට් කරන විට, ප්ලේන් එක තරමක් වටකුරු හැඩයකට වෙනස් කිරීමට හෝ ප්ලේට් කිරීම සඳහා මැට් මතුපිටක් සෑදීමට උත්සාහ කරන්න, මන්ද පැතලි හැඩය තුනී මධ්යයක් සහිත අසමාන තහඩුවක් සහ ප්ලේට් කිරීමේදී ඝන දාරයක් ඇති බැවිනි.එසේම, ප්ලේටින් ග්ලොස් වල ඒකාකාරිත්වය වැඩි කිරීම සඳහා, තරමක් පරාවලයික හැඩයක් ඇති පරිදි විශාල තහඩු මතුපිට ප්රදේශයක් සහිත ප්ලාස්ටික් කොටස් සැලසුම් කිරීමට උත්සාහ කරන්න.
D).ප්ලාස්ටික් කොටස්වල අවපාත සහ නෙරා යාම අවම කරන්න, මන්ද ගැඹුරු අවපාත ප්ලාස්ටික් ප්ලේට් කිරීමේදී ප්ලාස්ටික් හෙළි කිරීමට සහ නෙරා යාමෙන් දැවී යාමට නැඹුරු වේ.වලේ ගැඹුර වල පළලින් 1/3 නොඉක්මවිය යුතු අතර පතුලේ වටකුරු විය යුතුය.ග්රිල් එකක් ඇති විට, කුහරයේ පළල කදම්භයේ පළල හා ඝනකමෙන් 1/2 ට වඩා අඩු විය යුතුය.
E).ආලේපිත කොටසෙහි ප්රමාණවත් සවි කිරීම් ස්ථාන නිර්මාණය කළ යුතු අතර එල්ලෙන මෙවලම සමඟ ස්පර්ශක පෘෂ්ඨය ලෝහ කොටසට වඩා 2 සිට 3 ගුණයකින් විශාල විය යුතුය.
F).ප්ලාස්ටික් කොටස් අච්චුවේ ආලේප කළ යුතු අතර ප්ලේට් කිරීමෙන් පසු ඩිමොල්ඩ් කළ යුතුය, එබැවින් ප්ලේටඩ් කොටස්වල මතුපිට හැසිරවීමට හෝ විකෘති කිරීමේදී බල කිරීමෙන් තහඩු බන්ධනයට බලපාන්නේ නැති පරිදි ප්ලාස්ටික් කොටස් පහසුවෙන් ඉවත් කිරීමට සැලසුම සහතික කළ යුතුය. .
G).ගැටගැසීම අවශ්ය වූ විට, දණගැස්වීමේ දිශාව ඩිමෝල්ඩින් දිශාවට සමාන විය යුතු අතර සරල රේඛාවකින් විය යුතුය.ගැට ගැසුණු ඉරි සහ ඉරි අතර දුර හැකි තරම් විශාල විය යුතුය.
H).ප්ලාස්ටිං අවශ්ය ප්ලාස්ටික් කොටස් සඳහා, ප්ලේට් කිරීමට පෙර ප්රතිකාරයේ විඛාදන ස්වභාවය නිසා හැකිතාක් ලෝහ ආවරණ භාවිතා කිරීමෙන් වළකින්න.
මම).ප්ලාස්ටික් කොටසෙහි මතුපිට ඉතා සුමට නම්, එය ප්ලේටින් ස්ථරය සෑදීමට හිතකර නොවේ, එබැවින් ද්විතියික ප්ලාස්ටික් කොටසෙහි මතුපිට යම් මතුපිට රළුබවක් තිබිය යුතුය.
3. අච්චු නිර්මාණය සහ නිෂ්පාදනය
ඒ).අච්චු ද්රව්ය බෙරිලියම් ලෝකඩ මිශ්ර ලෝහයෙන් නොකළ යුතුය, නමුත් උසස් තත්ත්වයේ වැකුම් වාත්තු වානේ.කුහරයේ මතුපිට 0.21μm ට අඩු අසමානතාවයකින් අච්චුවේ දිශාව දිගේ දර්පණ දීප්තියට ඔප දැමිය යුතු අතර මතුපිට දෘඩ ක්රෝම් වලින් ආලේප කළ යුතුය.
බී).ප්ලාස්ටික් කොටසෙහි මතුපිට අච්චු කුහරයේ මතුපිට පරාවර්තනය කරයි, එබැවින් විද්යුත් ප්ලාස්ටික් කොටසෙහි අච්චු කුහරය ඉතා පිරිසිදු විය යුතු අතර අච්චු කුහරයේ මතුපිට රළුබව මතුපිට මතුපිට රළුබවට වඩා ශ්රේණි 12 ක් වැඩි විය යුතුය. කොටස.
C).කොටස් කරන ලද මතුපිට, විලයන රේඛාව සහ හර ඉන්ලේ රේඛාව සැලසුම් නොකළ යුතුය.
D).කොටසෙහි ඝනකම කොටසෙහි දොරටුව සැලසුම් කළ යුතුය.කුහරය පිරවීමේදී දියවීම ඉක්මනින් සිසිල් වීම වැළැක්වීම සඳහා, ගේට්ටුව හැකි තරම් විශාල විය යුතුය (සාමාන්ය එන්නත් අච්චුවට වඩා 10% පමණ විශාල), වඩාත් සුදුසු වන්නේ ගේට්ටුවේ සහ ස්පෘයේ වටකුරු හරස්කඩක් සහ දිග sprue කෙටි විය යුතුය.
E).කොටසෙහි මතුපිට වායු සූතිකා සහ බුබුලු වැනි දෝෂ වළක්වා ගැනීම සඳහා පිටවන සිදුරු සැපයිය යුතුය.
F).අච්චුවේ සිට කොටස සුමටව මුදා හැරීම සහතික කිරීම සඳහා ඉෙජක්ටර් යාන්ත්රණය තෝරා ගත යුතුය.
4.ප්ලාස්ටික් කොටස් සඳහා ඉන්ජෙක්ෂන් මෝල්ඩින් ක්රියාවලියේ තත්ත්වය
ඉන්ජෙක්ෂන් මෝල්ඩින් ක්රියාවලියේ ලක්ෂණ නිසා අභ්යන්තර ආතතීන් නොවැළැක්විය හැකි නමුත් ක්රියාවලි තත්වයන් නිසි ලෙස පාලනය කිරීම අභ්යන්තර ආතතීන් අවම වශයෙන් අඩු කර කොටස් සාමාන්ය භාවිතය සහතික කරයි.
පහත සඳහන් සාධක ක්රියාවලිය කොන්දේසි අභ්යන්තර ආතතිය බලපායි.
ඒ).අමු ද්රව්ය වියළීම
ඉන්ජෙක්ෂන් මෝල්ඩින් ක්රියාවලියේදී, ප්ලේටින් කොටස් සඳහා භාවිතා කරන අමුද්රව්ය ප්රමාණවත් තරම් වියළී නොමැති නම්, කොටස්වල මතුපිට පහසුවෙන් වායු සූතිකා සහ බුබුලු නිපදවන අතර එමඟින් ආලේපනයේ පෙනුම සහ බන්ධන බලය කෙරෙහි බලපෑමක් ඇති කරයි.
බී).අච්චු උෂ්ණත්වය
අච්චුවේ උෂ්ණත්වය තහඩු ස්ථරයේ බන්ධන බලයට සෘජු බලපෑමක් ඇත.අච්චුවේ උෂ්ණත්වය ඉහළ මට්ටමක පවතින විට, දුම්මල හොඳින් ගලා යන අතර, එම කොටසෙහි අවශේෂ ආතතිය කුඩා වන අතර, එය ප්ලේටින් ස්ථරයේ බන්ධන බලය වැඩි දියුණු කිරීම සඳහා හිතකර වේ.අච්චුවේ උෂ්ණත්වය ඉතා අඩු නම්, ප්ලේට් කිරීමේදී ලෝහය තැන්පත් නොවන පරිදි, අන්තර් ස්ථර දෙකක් සෑදීමට පහසුය.
C).සැකසුම් උෂ්ණත්වය
සැකසීමේ උෂ්ණත්වය ඉතා ඉහළ නම්, එය අසමාන හැකිලීමට හේතු වන අතර එමඟින් පරිමාවේ උෂ්ණත්ව ආතතිය වැඩි වන අතර මුද්රා තැබීමේ පීඩනය ද ඉහළ යනු ඇත, සුමට ඩිමෝල්ඩින් සඳහා දිගු සිසිලන කාලයක් අවශ්ය වේ.එබැවින්, සැකසුම් උෂ්ණත්වය ඉතා අඩු හෝ වැඩි නොවිය යුතුය.ප්ලාස්ටික් ගලා යාම වැළැක්වීම සඳහා තුණ්ඩයේ උෂ්ණත්වය බැරලයේ උපරිම උෂ්ණත්වයට වඩා අඩු විය යුතුය.කුට්ටි, ගල් හා අනෙකුත් දෝෂ නිෂ්පාදනය වැළැක්වීම සහ දුප්පත් ප්ලේටිං සංයෝජනයක් ඇති කිරීමට හේතු වන පරිදි, අච්චු කුහරය තුලට සීතල ද්රව්ය වැළැක්වීම සඳහා.
D).එන්නත් කිරීමේ වේගය, කාලය සහ පීඩනය
මෙම තුන හොඳින් ප්රගුණ නොකළහොත්, එය අවශේෂ ආතතිය වැඩි වීමට හේතු වේ, එබැවින් එන්නත් කිරීමේ වේගය මන්දගාමී විය යුතුය, එන්නත් කිරීමේ කාලය හැකි තරම් කෙටි විය යුතුය, සහ එන්නත් පීඩනය වැඩි නොවිය යුතුය, එමඟින් අවශේෂ අඩු කරයි. ආතතිය.
E).සිසිලන කාලය
අච්චුව විවෘත කිරීමට පෙර අච්චු කුහරයේ අවශේෂ ආතතිය ඉතා අඩු මට්ටමකට හෝ ශුන්යයට ආසන්න වන පරිදි සිසිලන කාලය පාලනය කළ යුතුය.සිසිලන කාලය ඉතා කෙටි නම්, බලහත්කාරයෙන් ඉවත් කිරීම කොටසෙහි විශාල අභ්යන්තර ආතතීන් ඇති කරයි.කෙසේ වෙතත්, සිසිලන කාලය ඉතා දිගු නොවිය යුතුය, එසේ නොමැති නම් නිෂ්පාදන කාර්යක්ෂමතාව අඩු වනු ඇත පමණක් නොව, සිසිලන හැකිලීම ද කොටසෙහි අභ්යන්තර සහ පිටත ස්ථර අතර ආතන්ය ආතතිය ඇති කරයි.මෙම අන්ත දෙකම ප්ලාස්ටික් කොටසෙහි ප්ලේටරයේ බන්ධනය අඩු කරනු ඇත.
F).මුදා හැරීමේ නියෝජිතයින්ගේ බලපෑම
ආලේපිත ප්ලාස්ටික් කොටස් සඳහා මුදා හැරීමේ කාරක භාවිතා නොකිරීම වඩාත් සුදුසුය.ප්ලාස්ටික් කොටසෙහි මතුපිට ස්ථරයට රසායනික වෙනස්කම් ඇති කර එහි රසායනික ගුණාංග වෙනස් කළ හැකි බැවින් තෙල් මත පදනම් වූ මුදා හැරීමේ නියෝජිතයින්ට අවසර නැත, එහි ප්රතිඵලයක් ලෙස ප්ලේටින් දුර්වල බන්ධන ඇති වේ.
මුදා හැරීමේ කාරකයක් භාවිතා කළ යුතු අවස්ථා වලදී, අච්චුව මුදා හැරීම සඳහා ටැල්කම් පවුඩර් හෝ සබන් වතුර පමණක් භාවිතා කළ යුතුය.
ප්ලේට් කිරීමේ ක්රියාවලියේ විවිධ බලපෑම් සාධක හේතුවෙන් ප්ලාස්ටික් කොටස් විවිධ මට්ටමේ අභ්යන්තර ආතතියට ලක් වන අතර, එය ආලේපනයෙහි බන්ධනය අඩු කිරීමට හේතු වන අතර, ආලේපන බන්ධනය වැඩි කිරීම සඳහා ඵලදායී පශ්චාත් ප්රතිකාරයක් අවශ්ය වේ.
වර්තමානයේ, තාප පිරියම් කිරීම සහ මතුපිට නිම කිරීමේ නියෝජිතයන් සමඟ ප්රතිකාර කිරීම ප්ලාස්ටික් කොටස්වල අභ්යන්තර ආතතීන් ඉවත් කිරීම සඳහා ඉතා හොඳ බලපෑමක් ඇත.
මීට අමතරව, ආලේපිත කොටස් ඉතා ප්රවේශමෙන් ඇසුරුම් කර පරීක්ෂා කිරීම අවශ්ය වන අතර, ආලේපිත කොටස්වල පෙනුමට හානි නොකිරීම සඳහා විශේෂ ඇසුරුම් සිදු කළ යුතුය.
Xiamen Ruicheng Industrial Design Co., Ltd සතුව ප්ලාස්ටික් ආලේපනය පිළිබඳ පොහොසත් අත්දැකීම් ඇත, ඔබට කිසියම් අවශ්යතාවයක් ඇත්නම් අප හා සම්බන්ධ වීමට නිදහස් වන්න!
පසු කාලය: පෙබරවාරි-22-2023